The Waterloo Boy Restoration Project
Phase 5 - Jan. 5, '98 to Jan. 28, '98
Now that all babbitt surfaces, i.e. the bearing itself, the inside thrust surfaces and outer ends, have been machined, the main caps are removed and the process of final scraping is done. The crankshaft is laid into position and the shims and caps are reinstalled as far as possible. Since the bearings are still slightly undersized, the crank will not completely fit on the first try. The crankshaft is turned by hand which leaves marks in the babbitt. With the crankshaft removed, these marks or “high spots” in the babbitt are scraped down very slightly using a bearing scraper. These sharp, triangular scrapers remove only a few tenths of a thousandth of an inch at a time. The crank is reinstalled again with the caps and again turned. This process is repeated until a uniform fit is attained and the rotation of the crankshaft in the oiled mains is smooth and fairly easily accomplished.
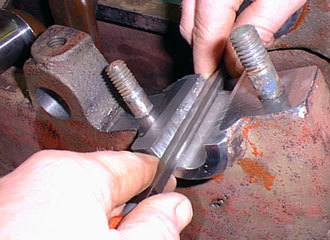
The final process to be done (not shown) is the drilling out of the grease cup holes and the cutting of lubrication grooves in the bearing surfaces. These are simple straight grooves cut in line with the bearing to distribute the grease from the grease cup along the width of the bearing. With the fabrication of 4 new main bearing studs, the restoration of the mains is now complete.
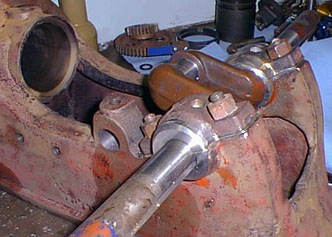
Back to the head work. The valves were in fair condition, at least the heads. The stems had seen better days and needed replacing. Since the valve are ‘two piece’ units, the old stems were removed and replaced. Once the head is placed on the stem, the protruding stem is peened on top of the head to hold it in place.
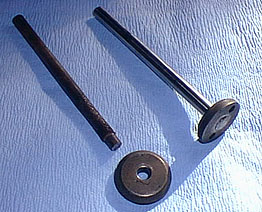
The valve guides were also worn and needed to be reamed round and to the proper size of the new valve stems. This was really the only part of the engine that showed any real wear.
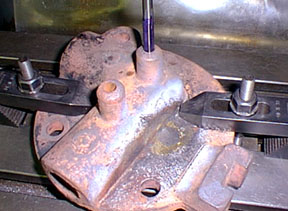
The refurbished valves were machine ground to bring the heads back concentric with the stems and to remove any pitting, which there was surprisingly very little of. The ground valves are now ready to be lapped.
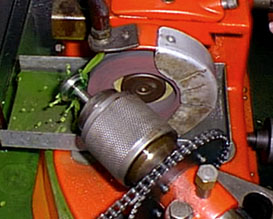
The valve seats in the head did not show any signs of ever being ground since the engine was first built in 1911. This was also true of the valves themselves. Here, three different angles are ground into each seat to produce a narrow seat area, something that was not normally done. The narrow seats tend to seal better and resist becoming leaky due to deposits (carbon) chipping off and sticking to the seat.
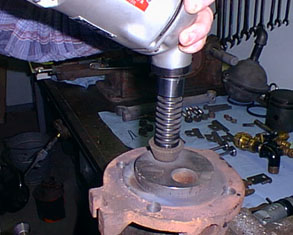